Bubble-Tight-Dampers-FAQs
Bubble-Tight-Dampers-FAQs
Link text :
Learn More
Select a Card/Question Answer :
Card
Display order :
1
Learn about our testing and compliance policies and more for bubble tight dampers.
faqcategories :
- Dampers FAQs
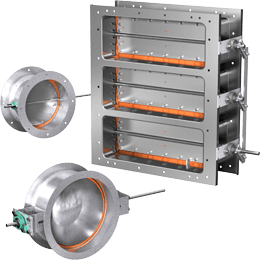
Related pages :
Bubble Tight Dampers FAQs
from