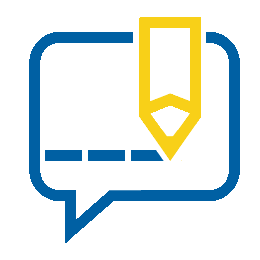
Understanding the basic Operation of a Variable Volume Lab Exhaust System
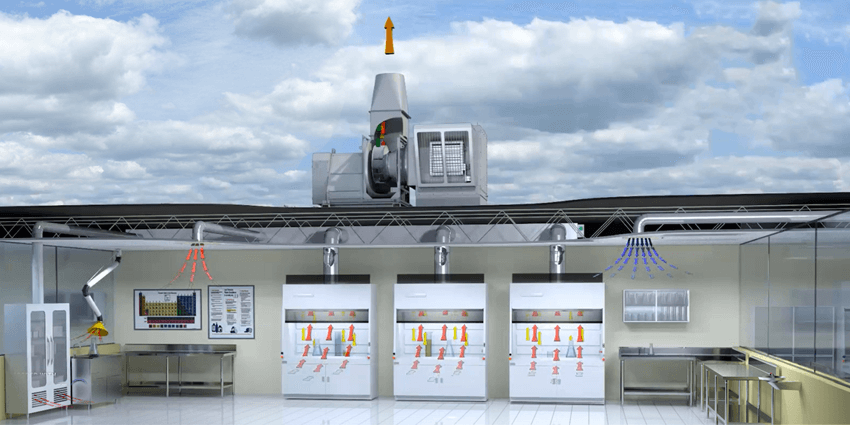
Lab ventilation systems are traditionally high users of energy based on the objectives of:
- Safely exhausting fumes and odors from the lab space
- Expelling fume and odor contaminants above the facility to prevent entrainment back into the lab or neighboring facilities
- Supplying 100% fresh make-up air to maintain appropriate pressures in the lab at the desired room temperature and humidity levels
The most common approach to address these exhaust and supply needs while reducing overall system energy is to utilize a basic variable air volume (VAV) system. VAV system design can be simple as shown below where there is a single exhaust fan that is tied to three variable volume chemical fume hoods. A VAV system can be much larger with three or more fans that stage on and off based on lab demand. Regardless of the lab size, each VAV fume hood has an exhaust valve to control flow through the hood. Hoods with common research generally merge to a manifolded exhaust duct that feeds the roof mounted fan(s). The lab space also has a fresh air a supply duct with a modulating valve to adjust the volumetric flow of air.
![]() |
Figure 1 |
There are three control loops that are maintained to operate a VAV lab system. Figure 1.
- Pressurization of the space – It is typical for labs to operate at negative pressure to contain fumes and odors. To do this, our control system is set to allow more exhaust air than supply air. The amount of exhaust needed ties to the amount of conditioned supply air that is needed.
- Chemical fume hood flow – The VAV chemical fume hood includes a valve that varies the airflow based on sash position. Exhaust velocities through the hood will vary by application, but 100 ft/min is common. As the sash opens, sash sensors and/or velocity sensors provide a signal for the valve to open to attain the desired airflow and safe hood velocity. As the sash closes, the individual valve will close to a specific level to maintain the desired velocity.
- Duct pressure – Monitoring duct pressure between the chemical fume hoods or other exhaust air entries ensures the system has appropriate negative pressure to keep the lab space negative when VAV hood sashes open abruptly. Duct pressure also is monitored to prevent too much negative pressure, which can potentially damage the exhaust valves or the duct work.
![]() |
Figure 2 |
The bypass air plenum is positioned below an inline fan or adjacent to a scroll-style centrifugal fume exhaust fan. It contains an isolation damper to disconnect the fan from the duct system when the fan is not in use. The bypass damper supplies outside air to the fan for when sashes are closed and negative pressure in the duct increases. Using this bypass supply air reduces the air coming from the exhaust system when hood demand is less. The benefits include:
The opposite occurs when sashes begin to open. The VAV hood valve opens, duct pressure becomes less negative, and the bypass dampers start closing. This action pulls more air from the lab exhaust system and the make-up air begins to ramp up to ensure proper system pressure.
The following video walks through the interaction of this system using Greenheck’s Virtual Lab.
Summary
Lab exhaust systems are needed to provide a safe environment in and around lab facilities. The requirements of managing chemical fume exhaust, creating high-velocity plumes, and dealing with 100% air can lead to significant energy usage. Using a VAV lab system in conjunction with proper training for lab users to shut down their sashes when not in use, it is possible to have a safe environment while also reducing overall energy consumption.
from