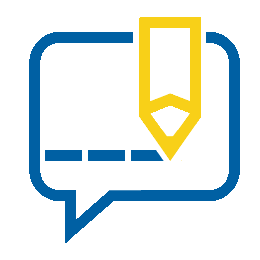
Evaluating Finish Coat Processes for Grilles, Registers, and Diffusers
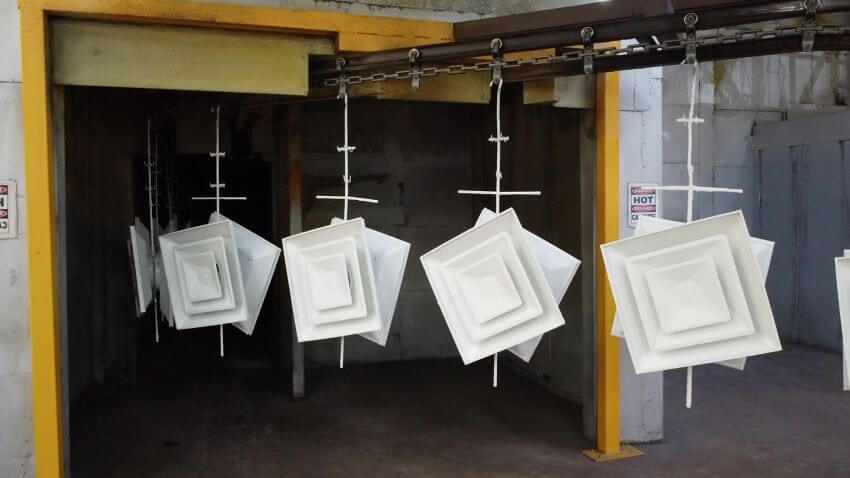
Grilles, registers, and diffusers (GRD) are an afterthought for most people until something like rust ruins the aesthetics of a space. GRD products corrode due to a variety of reasons. The primary reason is humidity and dust particles finding untreated
metal on the product instead of being encapsulated by the finish coat. No industry standards currently exist for best practices in applying finish coats to GRD products; however, manufacturers test their finishes to specific ASTM standards to ensure
that the paint is corrosion-resistant and withstands impacts without damage. The industry currently uses three processes for applying the finish coat to GRD products. Two have proven value, while the use of another continues despite technological
advances.
On-Site Application
Applying a finish coat on site predates the other two processes and is quite simple. The end user or field installer paints the finish coat on-site. The reasoning behind
an on-site finish method often is to match a specific color to the overall design of the space to GRD products. Some may also think this finish coat method can save money by applying the finish themselves. Both assumptions are generally incorrect.
The on-site or do-it-yourself method seldom achieves the desired finish compared to a factory-applied finish and can detract from the overall aesthetics of the space. The GRD product requires a clean surface for the finish coat to adhere properly.
Failure to clean the surface will result in the coating peeling away from the surface. The finish coat is not as strong as a factory-applied coating and will chip or scratch more easily. Furthermore, most companies that supply GRD products have elaborate
color-matching capabilities, allowing them to ensure the end users get the precise color to go with the rest of the interior design. The bottom line is an on-site finish application is less durable, probably won’t save any money, nor will it
provide a more accurate color match than a finished product from the factory.
Powder Coating
Many companies that manufacture GRD products use a powder coating. The powder coating process is quite simple. The trick to applying a good finish coat begins with cleaning the metal surface of the
GRD products to remove dirt, oils, and any metal shavings left from the manufacturing process.
Powder coating systems often use a cleaning stage where the metal is washed with solvents to remove surface contaminants. The rinse process removes the solvents and leaves a clean surface that receives a conversion coating next. This microthin conversion coating provides added resistance to corrosion and promotes paint adhesion. The finish coat is an electrostatically-charged paint powder that attaches to the metal, forming a resilient bond. Manual and robotic sprayers often apply the coating. The coated parts then move to a temperature-controlled oven where the powder coat bakes onto the metal surface. This process creates a long-lasting, strong, durable finish able to resist scratching and chipping under normal conditions.
Powder coating products continue to grow in popularity throughout many industries, including HVAC, primarily because of their quality and durability. However, its use may create some challenges for complex parts. The powder coating process can leave exposed metal on some GRD products with intricate designs, where spray guns might miss and expose the product to corrosion.
e-Coating
The third finish coat process is e-coating. E-coating shares similar steps with powder coating that include:
- Cleaning stages
- Rinsing
- Application of a bonding and corrosion-resistant chemical
- Baking in a temperature-controlled oven
However, e-coating differs from powder coating in its finish coat application. We attach the GRD products to a conveyor line that submerges the products in a large tank containing the finish coat. The metal conveyor line receives an electric current that
conducts electricity through the metal GRD products hung on the paint line hooks. The tank holds the water-based liquid paint solution. The paint has an opposite electrical charge, so the paint adheres to the metal. All products then move on to the
oven, where, like powder coating, the finish bakes onto the product surface. This baking process causes the paint molecules to cross-link, forming a resilient, durable finish with the same qualities as a powder-coated product. However, there is one
difference. Unlike powder coating, where manual or robotic sprayers can miss spots, e-coating gets into hard-to-reach areas on complex parts, ensuring no metal has exposure to the elements.
Selecting the Best Finish for GRD Products
Powder coating and e-coat finishes will provide the best finish for GRD products. Technology advances also make color-matching from the factory easy and eliminate the need to apply a finish
coat in the field, saving time, aggravation, and money. Greenheck offers a complete line of GRD products we currently e-coat to provide you with many years of reliable use. Contact your local Greenheck representative for more information.
from